Be intentional about including the following tactics in your new year marketing strategy As 2025…
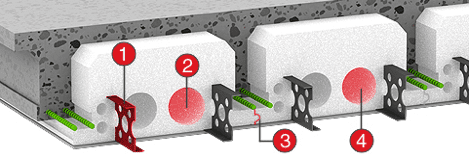
I Don’t Have Anything To Say … (about My Industrial Marketing)
20 great blog post ideas for February, if you are an ICF floor and roof manufacturer.
If you want to be successful at industrial marketing, you must communicate. Sounds like common sense wisdom, right? We’ve found very few industries have the audience or the product needed to take advantage of a high level of industrial marketing communications. The building materials industry is one of those that have an unlimited amount of content. This post will focus on what the insulated concrete form industry can say (or has to say) in one month, specifically the insulated concrete form system for floors and roofs. If they do, we can guarantee results. Did we tell you it has a snowball effect?
- Insulating Concrete Form or (ICF) is a system of formwork for reinforced concrete that stays in place as a permanent interior and exterior substrate for walls, floors, and roofs, this means less labor to set up the forming. No crane may be needed, saving money on the job site. Photo of Insul-Deck detail features.
- ICF construction has become commonplace for both low-rise commercial and high-performance residential construction as more stringent energy efficiency and natural disaster resistant building codes are adopted.
- The ICF construction technique was first developed in Europe following World War II as an inexpensive and durable way to rebuild damaged structures. Every job site that uses it can tell the same story.
- The first patent for an insulated stay-in-place formwork for concrete was registered in the early 1940s using recycled waste wood and cement as the insulating material. This patent was registered by August Schnell and Alex Bosshard in Switzerland. This system could be a great sustainable alternative rather than the expanded polystyrene commonly used today. Photo of Piero Cretti – Insul-Deck Inventor U.S. Patent Number 5,792,481, August 11, 1998.
- The adoption of ICF construction has steadily increased since the 1970s, though it was initially hampered by lack of awareness, building codes, and confusion caused by many different manufacturers selling slightly different ICF designs rather than focusing on industry standardization. ICF construction is now part of most building codes and accepted in most jurisdictions, in the developed world. What a great story to tell? How many other building materials can tell a growing story?
- Reinforcing steel bars (rebar) are usually placed inside the forms before concrete is poured to give the concrete flexural strength, similar to bridges and high-rise buildings made of reinforced concrete. It’s fun to show the incredible strength and amazing cantilevered roofs possible with steel and even carbon fiber reinforced concrete. Wow! Always is an attention getter. The photo of Casa Bella Verde demonstrates a huge cantilevered patio and it’s going for LEED Platinum!
- After the concrete has cured, the forms are left in place permanently to provide a variety of benefits, depending on materials used:
• Thermal insulation
• Soundproofing
• Surface burning characteristics
• Space to run electrical conduit and plumbing. The form material on one side of the floor or roof and even inside the form can easily accommodate electrical and plumbing installations.
• Backing for drywall or other finishes on the interior and stucco, brick, or other siding on the exterior
• Improved indoor air quality
• Regulates humidity levels and mitigates mold growth - Energy efficiency benefits:
• Minimal, if any, air leaks, which improves comfort and reduces heat loss compared to walls without a solid air barrier
• High thermal resistance R-17; this results in saving energy compared with uninsulated masonry
• Continuous insulation without thermal bridges or “insulation gaps”, as is common in framed construction
• Thermal mass, when used well and combined with passive solar design, can play an important role in further reductions in energy use, especially in climates where it’s common to have outside temperatures swing above inside temperatures during the day and below at night. Photo of the Nutter Residence. - Strength benefits:
• Insulating concrete forms create a structural concrete wall, either monolithic or post and beam, that is up to ten times stronger than wood framed structures.
• Structural integrity for better resistance to forces of nature, compared to framed walls.
• The components of ICF systems — both the poured concrete and the material used to make the ICF — do not rot when they get wet. - Sound absorption benefits:
ICF walls have much lower rates of acoustic transmission. Standard thickness ICF walls have shown sound transmission coefficients (STC) between 46 and 72 compared to 36 for standard fiberglass insulation and drywall. The level of sound attenuation achieved is a function of wall thickness, mass, component materials and air tightness. Photo of cinema complex built with Insul-Deck. - Fire protection benefits:
ICF walls can have four- to six-hour fire resistance rating and negligible surface burning properties - Indoor air quality benefits:
ICF walls can regulate humidity levels, mitigate the potential for mold and facilitate a more comfortable interior while maintaining high thermal performance. - Environmental sensitivity benefits:
ICF walls can be made with a variety of recycled materials that can minimize the environmental impact of the building. - Building process benefits:
ICF construction is less demanding, owing to its modularity. Less-skilled labor can be employed to lay the ICF forms, though careful consideration must be made when pouring the concrete to make sure it consolidates fully and cures evenly without cracking. Unlike traditional wood beam construction, no additional structural support other than temporary scaffolding is required for openings, doors, windows, or utilities, though modifying the structure after the concrete cures requires special concrete cutting tools. Photo from Insul-Deck Green Building examples. - Floor and foundation benefits:
ICF walls can be tied into the floor or roof forms with embedded rebar dowels connecting them to the foundation. - ICF decking is becoming an increasingly popular addition to general ICF wall construction. ICF decking weighs up to 40% less than standard concrete flooring and provides superior insulation. ICF decking can also be designed in conjunction with ICF walls to form a continuous monolithic structure joined together by rebar. ICF deck roofs are becoming more common as additives allow you to pour concrete on an angled surface.
- Plumbing and conduit is easy with ICF:
Plumbing and electrical conduit can be placed inside the forms and poured into place, though settling problems could cause pipes to break, creating costly repairs. For this reason, plumbing and conduit are usually embedded directly into the foam before the wall coverings are applied. A hot knife is commonly used to create openings in the foam to lay piping and cabling, while ICFs made from other materials are typically cut or routed with simple carpentry tools. Photo from Quad-Deck. - Cost can be a benefit for some projects:
The initial cost of using ICFs rather than conventional construction techniques is sensitive to the price of materials and labor, but building using ICF can generally add 3 to 5 percent in construction cost over building using wood frame. In most cases, ICF construction will cost about 40% less than conventional construction because of the labor savings from combining multiple steps into one step. - ICF construction can allow up to 60% smaller heating and cooling units to service the same floor area, which can cut the cost of the final house by an estimated $0.75 per square foot. So, the estimated net extra cost can be as much as $0.25 to $3.25. ICF homes can also qualify for tax credits, further lowering the costs. The Kinsman residence shown, used ICF and only heats with the hot water solar panels on the roof.
- ICF buildings are less expensive over time as they require less energy to heat and cool the same size space compared to a variety of other common construction methods. Additionally, insurance costs can be much lower as ICF homes are much less susceptible to damage from earthquakes, floods, hurricanes, fires, and other natural disasters. Maintenance and upkeep costs are also lessened as ICF buildings do not contain wood, which can rot over time or be attacked by insects and rodents.
Whew! That’s a lot of blogging. But rust never sleeps and neither does great web content. These posts will be the gift that never stops giving. This is the only way an industrial marketer can get a good night’s sleep. Take us up on the challenge for your product, you won’t regret it. If you can’t muster this much content, a very close-to-the-vest managed search engine adwords program may be worth a try. Thanks to Wikipedia for the outline of this post.
If you liked this post, you may also like, “Hubspot: The Solution for “No Time” Marketing Communications.”